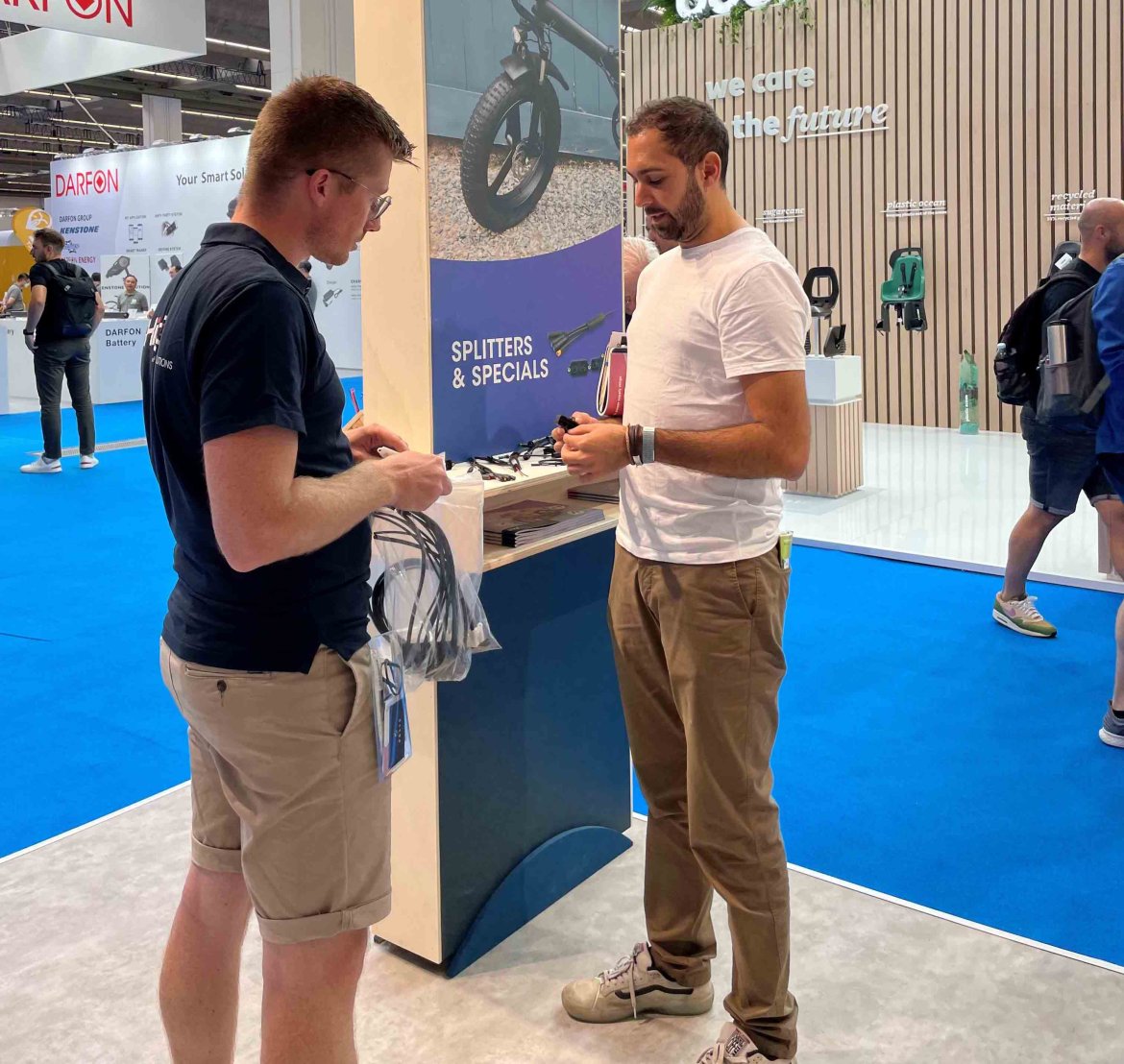
Customisation in e-bike connectors
Standard connectors just don't fit the widespread market anymore. Many of the new e-bike designs we come across require more complicated, tailor-made connections. We understand the importance of creating the right e-bike connector solution that perfectly matches each design or system. We don't settle for less.
With 10 years of experience in the E-bike market, our team knows how to guide you from your concept drawing to the final Higo e-bike connector design.
The options are endless. We are able to work out with you any kind of Higo splitter, cable harness or customised connector. You can also count on us to manage your full cabling project.
Customisation is Higo's core-business
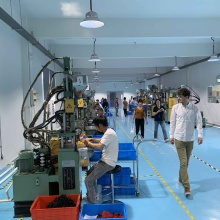
Full in-house manufacturing
In their production sites of 50.000m2 in total, Higo takes care of the complete cabling of any type of e-bike, cargo bike or e-moped. All connector related processes are manufactured in-house, from the production of cables, tooling and the single-handedly turning of contacts until the complete assembly of connectors. This makes it easier to monitor quality and it shortens the lead time substantially.
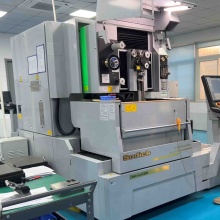
Investments in technology
Investments in emerging technologies like 3D printing and the automation of production processes further enhance Higo’s power to customise connector solutions to the needs of each customer without compromising lead times. This facilitates Higo in the manufacturing of splitters, harnesses and customised connectors with Higo and in combination with other connectors.
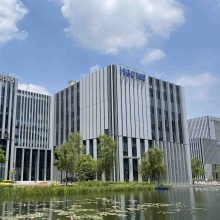
16 years of e-bike market experience
Higo has been the first manufacturer in the e-bike market to fully focus on the development of e-bike connectors. Throughout the 16 years of experience, it gained extensive experience in building up a complete range of standard as well as customised e-bike connectors. Today Higo is still a forerunner in the market and perfectly capable of fulfilling every e-bike connector need.
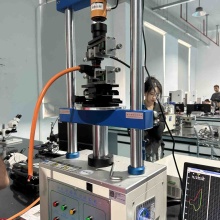
Quality & Testing
Higo uses high-quality plastics reinforced by fine glass fibers for the moulding process. It also works with spring-loaded, gold plated female contacts for high power connectors to ensure a 360° contact area between male and female contact. Higo is equipped with extensive electrical, mechanical, environmental testing and inspection equipment and it works according to ISO 9001, ISO 14001, IATF16949 and IPC quality standards.